IMPACT STUDY
MRO for Iraqi Naval Fleet
Naval Base Modernization IqN Fleet Management 80% Operational Readiness
Overview
In 2014, the Iraq Ministry of Defense (MinDef) awarded Swiftships the sole source 4 (four) year Continuous Lifecycle Support (CLS) program under Foreign Military Sales (FMS) contract via NAVSEA. Under the agreement, Swiftships managed the maintenance of all vessels operated by the IqN, including maintenance support and repairs. In addition to Ship Repair Facility (SRF), the contract provided technical expertise in preventative and planned maintenance, emergency repairs, and platform overhaul support services.
Swiftships overtook management and modernization of the existing Iraqi Naval Base at Umm Qasr, formerly known as the ITSAM camp, built by the US Coalition forces in 2009. Our team resided in-country inside the Iraqi Naval Base Camp, now known as “Camp Swift,” and managed the overall scope of IqN fleet maintenance. During the program, Swiftships kept Iraq Navy fleet vessels at industry benchmarkable 80% operational readiness.
This program was an additional award, as Swiftships relationship with Iraq Navy (IqN) started on 35m Patrol Boat program in 2009. In partnership with the US Naval Sea Systems Command (NAVSEA), Swiftships built and delivered 12 (twelve) 35m Patrol Boats designed for the IqN. The program earned a gold standard reputation due to Swiftships’ capability to deliver the vessels in 36 months, an extremely tight schedule for state-of-the-art 35m Patrol Boats designed and customized with features to suit their needs.
Highlights

Benchmarkable Results
The 80% Operational Readiness of the Iraqi Navy fleet achieved

USN Standards
Planning Yard (PY), Ship Repair Facility (SRF) and Quality Control (QC) process compliance to the highest ratings

Entire IqN Fleet Management
Continuous Lifecycle Support (CLS) for all Iraq Navy vessels and Umm Qasr Base management

Full Scope In-Country Support
From facilities modernization, process automation to resident SME and technical teams support
Scope
Swiftships scope of work included Naval Base modernization (Planning Yard), Ship Repair Facility (SRF) management and Continuous Lifecycle Support (CLS) services for entire Iraq Navy fleet in Umm Qasr. Swiftships implemented the strictest Quality Control system, provided a custom-built Computer Management Maintenance System (CMMS) for operations management, training and integrated logistics support. In addition, Swiftships managed the entire Facilities and Base Security with both Static and Dynamic security personnel.
Program included: Two (2) 62m offshore support vessels (OSVs), twelve (12) 35m Patrol Boats (PBs), twenty-Six (26) 40ft Defender Class Boats, one (1) drydock, one (1) syncrolift maintenance, one (1) dyno-facility, one (1) ship repair facility (SRF) to provide all port side activity, and three (3) warehouses.
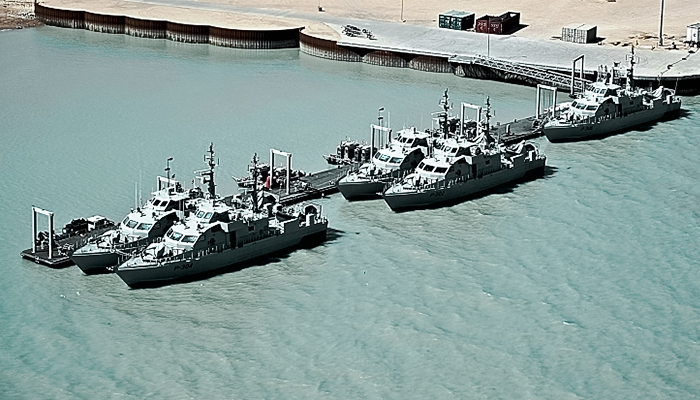
Approach
Modernization and Operational Readiness
At the initial stage Swiftships provided Planning Yard services to modernize existing facilities in Umm Qasr base. Swiftships advised and assisted with site layout and design for optimum Vessel Sustainment mission support against specific mission readiness. We helped design and built clean rooms to enable on-site engine overhauls. Swiftships also provided in-country training on all systems operations and systems preventative and mid to significant repairs.
Swiftships sustainment management team and Subject Matter Experts (SMEs) remained in Umm Qasr base to support IqN mission readiness for 24/7 operations. The team maintained all assets for over four (4) years, and helped to achieve the highest quality ratings from USN and keep IqN fleet operational readiness at over 80%.
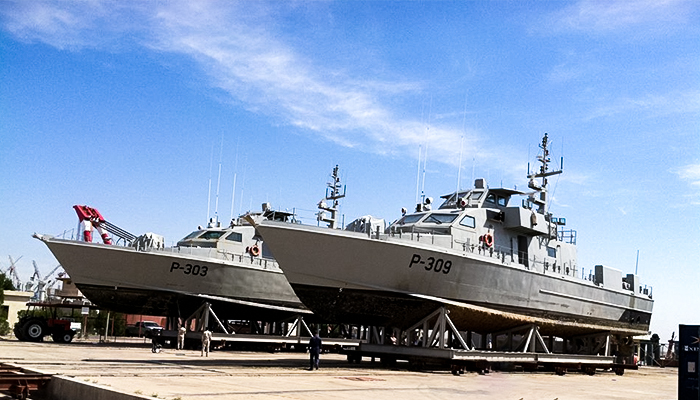
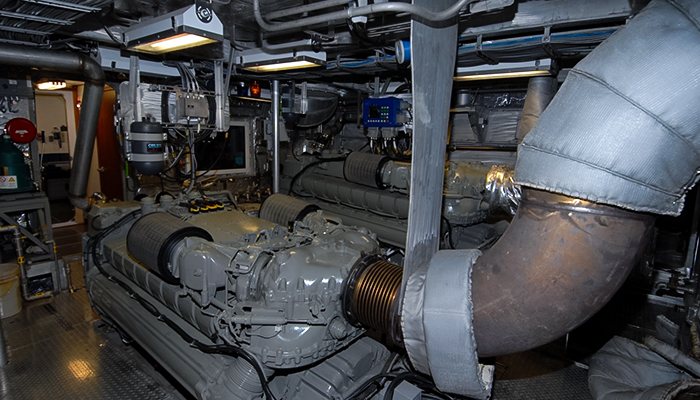
Quality Assurance
Swiftships Quality Assurance (QA) worked with US Navy Port Engineers on-site (in-country) to achieve the highest quality ratings for our customers most efficiently and cost-effectively.
We used our proven five (5) process methods:
- In-Process Testing and Inspection: Performed during Maintenance Cycle
- Level 1 Testing: General Systems Checks. Ensures piping, electrical, and mechanical systems are correctly installed
- Level 2 Testing: Dockside testing of all systems before getting underway. This testing is usually coupled with a river run to check propulsion and navigation equipment
- Level 3 Testing: Underway testing of all systems. This testing consists of an endurance run at speed to ensure propulsion plant is at an optimal level of performance. All designs are tested during this phase. If there are any defects during this phase, the contractor and sub-contractors will adjust and re-test
- Special Testing: These tests are generally explicitly created for unique equipment aboard the vessel, such as weaponry, RHIB units, cradles, etc. support
To ensure all defects were resolved, all testing procedures were approved and signed by the USN QA representative, Customer Representative, and Third-Party certifier representative. We also used our state-of-the-art online portal to track defects to minimize reoccurring issues.
Preventative and Corrective Maintenance Support
Swiftships used a custom-built Computer Management Maintenance System (CMMS) to manage material flow and control the stock from several warehouses and external sources . Swiftships worked with other client representatives, including but not limited to port engineer client maintenance support, and provided site/capabilities assessments and material condition assessments. The staging of vessels and associated materials were planned according to the level of deficiency and mitigation. A ship with high priority (Level 3 and 4) deficiencies were staged closer to the pier to ensure ease of crane, materials, and personnel access. The vessel with lower priority levels (Levels 1 and 2) was put back in the cue till resources were available.
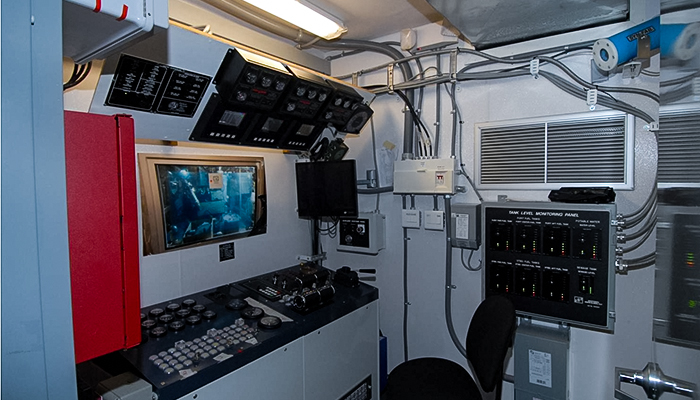
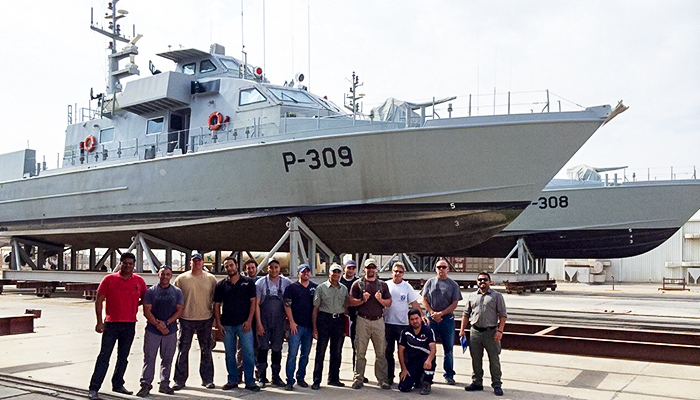
Training and Supply Chain Management
Swiftships also provided in-country training on all systems operations, and systems preventative and mid-to-significant repairs.Our on-site staff included, Purchasing and Integrated Logistics Support team members capable of supporting a full spectrum of material procurement from spares parts to preventative maintenance parts using in-country and worldwide supplier Network. Our in-country logistics personnel documented, labeled, and stored all incoming parts and conducted joint inventory. Our services included:
- In-country training
- Material/Equipment Procurement
- Country-specific Material/Spare Parts Requirements
- Warehousing and more
Results
Our in-country Planning Yard and MRO methodology has proven to be successful with customers worldwide. This program involved managing the maintenance of all vessels operated by the Iraqi Navy, including technical expertise in preventative and planned maintenance, emergency repairs, and platform overhaul support services. Swiftships was also responsible for modernizing the existing Iraqi Naval Base at Umm Qasr, as well as providing training and supply chain management. The program brought the operational readiness of the Iraqi Navy fleet up to a benchmark level of over 80%.
Our Planning Yard (PY), Facility Management, and Ship Repair Facility (SRF) program is standardized in line with USN’s standards, and it can be customized to fit any customer’s unique needs.
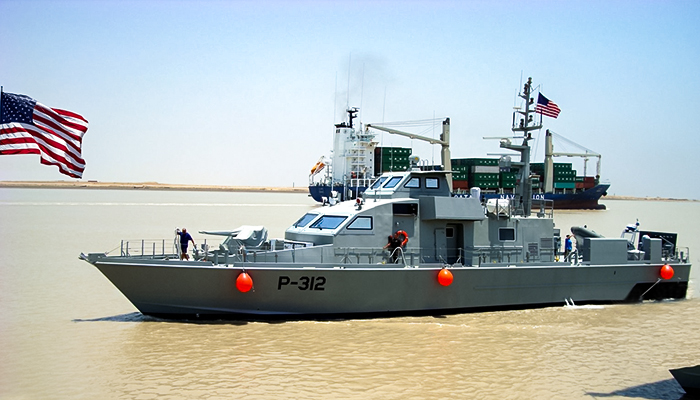